WPC処理、二硫化モリブデンショット、DLCコーティングをメインに、エンジンに用いられるさまざまな表面処理の種類と、実際の使用例をレポートします。
本記事でわかること
・メーカー各社が表面処理を採用する理由
・バイクへの使用例と活用法 ~旧車修理の最先端~
・エンジンパワーロスの原因と、効果的なフリクション低減ポイント
・学術的な根拠(研究論文や参考サイト)
「純正部品が手に入らない旧車部品を再生したり、少しでも長くエンジンを持たせることを考えた場合、表面処理をどのように活用すればいいか?」
をメインテーマとしています。
表面処理とは?
素材の表面の性質を向上させるためにおこなわれる加工のことです。
例:硬さ、耐摩耗性、潤滑性、耐食性、耐酸化性、耐熱性、断熱性、絶縁性、密着性、美観性など
目的や用途、素材などに応じた数多くの表面処理が存在します。
WPC処理や、二硫化モリブデンショット、DLCコーティングは表面処理の手法の一つです。工業、食品や医療など、いろんな分野で表面処理の技術が用いられています。
もちろん自動車や、バイクなどモータースポーツの分野でも採用されていて、効果も科学的に検証されています。
エンジンに表面処理をおこなうメリット
ひとことで言うと、フリクションを減らす事です。
フリクションとは摩擦のこと。2つ以上の物が合わさって、こすれ合う時に生じるのが摩擦です。
人間も2人以上になると摩擦が発生して、問題が起きますね。それと同じイメージです。
「なぜ、エンジンのフリクションを減らす事がそんなに重要なのか?」
順を追って、お伝えしていきます。
エンジンの40%が失われている
摩擦・潤滑を学問として研究している「トライボロジー」(tribology)があります。
トライボロジーは「摩擦学」や「潤滑学」と訳されています。
その歴史は古く、エジプトのピラミッド建造や、レオナルド・ダ・ヴィンチ(1452-1519)がいた時代にはすでに摩擦学の概念が存在していたと言われています。
現在も、トライボロジーは多岐の分野にわたって研究され続けています。
自動車やバイクはもちろん、ロケットや建設機械、家具や家電製品など、あらゆるところで活用されています。
トライボロジーの活用事例
タイヤ、ブレーキパッド、浴室の床や廊下、階段など(滑り止め)、競泳水着、電気シェーバー、スケートリンク、エンジンオイルなど潤滑油ほか
トライボロジーの研究によると、燃料エネルギーのうち、走行のために使われるのはおよそ14%といわれています。
つまり、エンジンのエネルギーの大部分がロスしているわけです。
さらに走行に使われるエネルギー14%のうち、約15%が摩擦によって失われているといわれています。
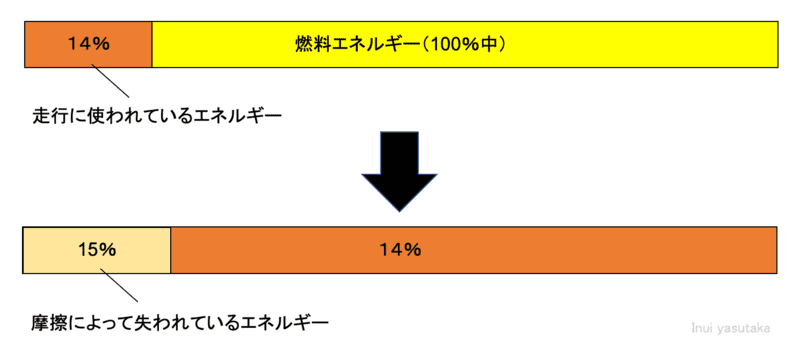
つまり摩擦を減らすことによって燃費向上につながるわけです。
とくにエンジンのなかで最も摩擦損失が大きいのが、シリンダー とピストン。摩擦損失は、少なくともエンジン全体の40%を占めると言われています。
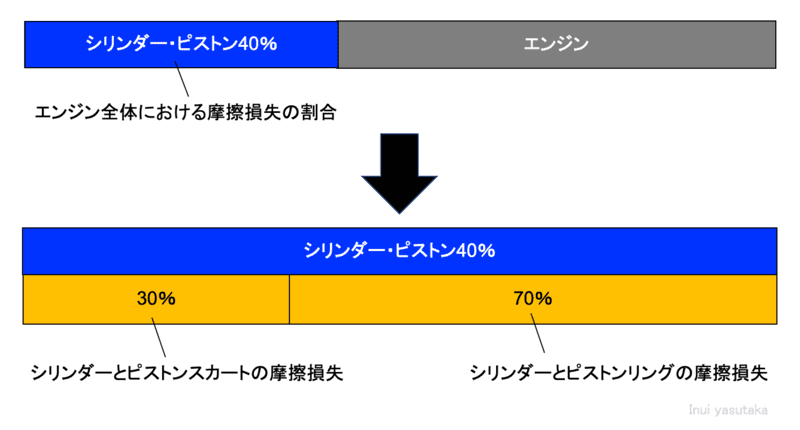
さらに40%の内訳を見ると、ピストンリングとシリンダーの摺動(しゅうどう)部分の摩擦損失が約70%、シリンダーと、ピストンスカートの摩擦損失は約30%になります。
ようするに、ピストンリングと、シリンダーの摺動(滑らせて動かすこと)が重要になってくるわけです。
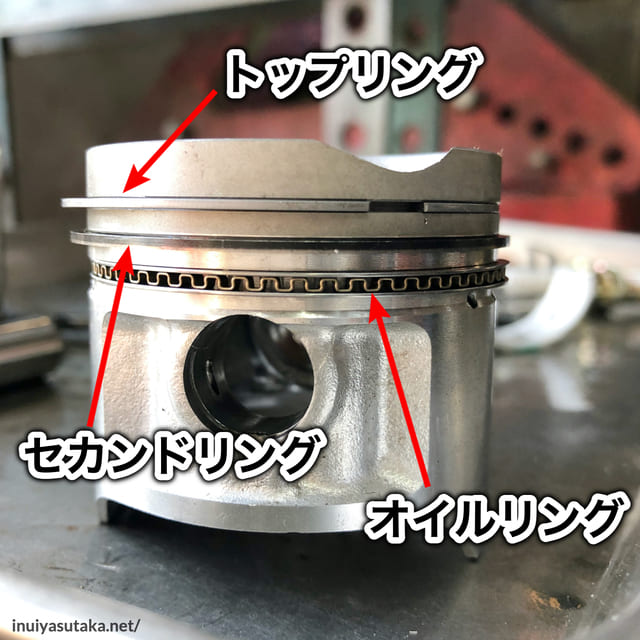
4スト空冷エンジンのピストン。一般的にピストンリングは3つあります。
(レースでは摩擦損失を減らすためにピストンリングを2本にします)
歴史的にピストンリング溝の異常摩耗や、凝着(ぎょうちゃく。溶けてくっついてしまう事)をふせいだり、ピストンスカートの摩擦を減らすため、さまざまなアプローチがおこなわれてきました。
お金とエネルギー
たとえば「収入を増やそう」と考えた場合、新たに収入を増やすより、むだ遣いを減らすほうが簡単です。1ヶ月で1万円のむだ遣いを減らしたら、1万円収入が増えるのと同じです。
1年だと、12万円収入が増える事になります。摩擦損失もこれとよく似ていて、むだを減らすことがいろんな面でプラスになるわけです。
エンジン焼き付きを防止する4つのポイント
「一体、なにがコンロッド焼き付きに大きく影響するのか?」
ホンダの研究論文によると、4ストエンジンの実験で興味深いことが判明しました。
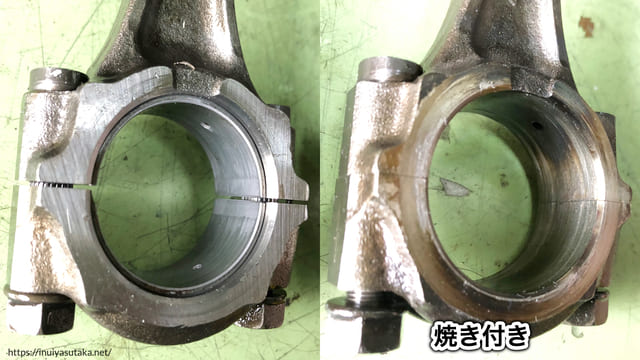
左側は正常なコンロッドとメタル。右側は焼きついたコンロッド。
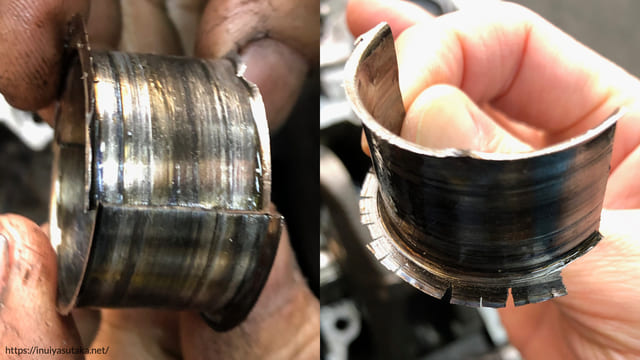
1,金属表面の仕上げ(面粗度)
面粗度が小さいほど耐焼き付き性が向上。逆に、面粗度が粗いと焼き付きやすい。
「面粗度」(めんそど)とは、かんたんに言うと、加工された金属表面の粗さです。
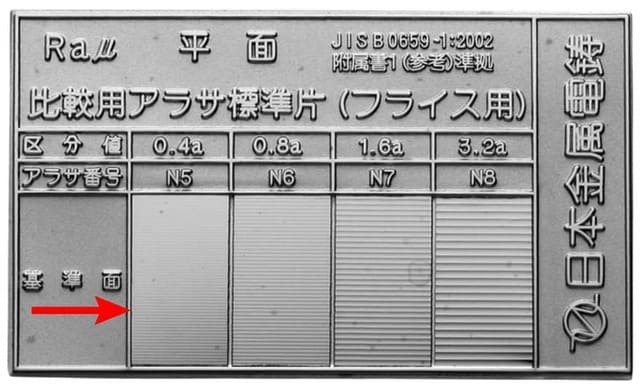
画像はあくまでイメージですが、左側ほど表面がこまかく、右へ行くほど表面が粗いです。
のちほどくわしくお伝えしますが、金属の表面はツルツルに見えても、拡大すると凹凸があります。
アプローチとして、
1,部品の製造・加工精度を高める
2,完成した部品に加工をおこなって凹凸を減らす
それが部品の摩耗を抑制したり、焼きつき防止、パワーの損失を減らすことにつながります。
たとえばエンジンを組み立てる場合、金属部品のバリを取り除いたりします。
表面処理も金属表面を滑らかにして、摺動性を向上させる(摩擦を減らす)ことで、耐焼き付き性能の向上につながるわけです。
2,メタルクリアランス
メタルには「クランクメタル」と「コンロッドメタル」があります。
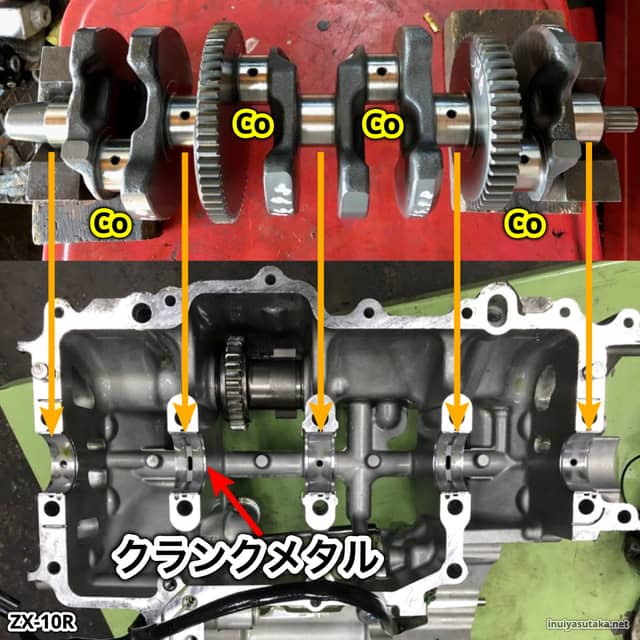
Coはコンロッド(とコンロッドメタル)が付くところ。オレンジ色の矢印はクランクメタルです。
メタルクリアランスが小さいと、オイル通路がせまくなって油量が低下、冷却不足により焼き付きが発生します。いっぽう、メタルクリアランスが大きすぎると、クランクシャフトが振れてトラブルが発生します。
最適なクリアランスで組むことが大事です。
エンジンオーバーホールなど、エンジンを組む場合も、各種クリアランスのマネジメントが重要です。
(形だけ正しく組んでも、クリアランスが不適切だと、焼き付きます)
絶版車・旧車の場合、クランクシャフトはもちろん、コンロッドやメタルも、車種によっては部品が手に入らないことがあります。
3,エンジン回転数
一般的に回転を上げると焼き付きやすいです。
4,エンジンオイル
一般的に油温が高いほど・低粘度ほど、焼き付きやすいです。
もし、エンジンオイルが無かったら?
エンジンオイルは、その名のとおりエンジン内部を潤滑することで摩擦抵抗を減らし、摩擦熱をおさえたり、金属の摩耗を防いでいます。
もし、エンジンオイルが無かったら、エンジンがエンジンとして機能せず、焼き付きます。
金属と金属が摩擦すると、高温の熱が発生します。その熱によって、焼き付くわけです。
https://inuiyasutaka.net/bikeblog/engineoil/
エンジンオイルについては、以下の記事でくわしく解説しています。
以上4つが、「焼き付きに大きく影響している」と判明したそうです。
ちなみに一般ライダーの場合、(すでにエンジンが組まれているため)面粗度やメタルクリアランスは、自分でどうすることもできません。
しかし暖機運転やエンジンの扱い方、エンジンオイル管理は、ライダーにコントロールできる余地があると思います。
エンジンのパワーロスや、焼き付きのメカニズムを知ると、「なぜ、メーカー各社がフリクションを減らす事に躍起になるのか」「どの箇所にフォーカスすべきか」理由がわかるというものです。
調子の良い状態をどれだけ長く維持できるか?
さらに付け加えると、
どんなに腕の良いショップでエンジンを組んでもらったとしても、その後の扱いかた次第で、エンジンの状態は大きく変わります。
不具合や故障があると、すぐバイクのせい、ショップのせいにするライダーが居ますが、ライダーの所作や、エンジンを観ていると、明らかに乗りかた、扱いかたに原因があるケースは少なくありません。
耳で体験 クランクシャフトの摩擦低減効果
摩擦を減らすことの重要性がわかったところで、実際に体験していただきましょう。
フリクション低減効果を耳で聴けるようにしました。
Before 焼き付いたクランクシャフトを修正して再利用したエンジン
After 同じエンジンに新品クランクシャフトを組んだ場合
両者を比較して聴くことで、摩擦の影響がいかに大きいか、実感できると思います。
(マフラーの排気音ではなく、エンジンの音にフォーカスしてください)
クランクシャフト交換前と交換後のエンジン音を比較
検証方法と解説
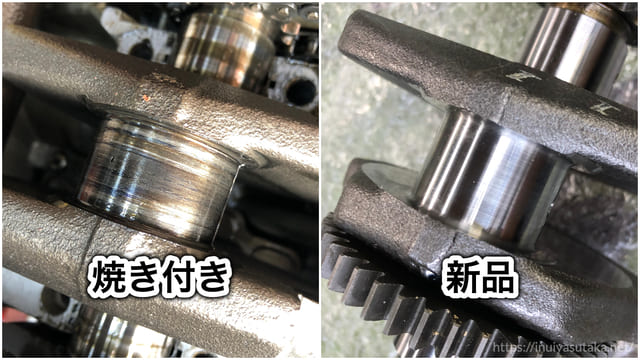
使用したエンジン:GSX400E(空冷 並列2気筒)
同じエンジンをプロのメカニックが分解・組み立てている。
1,焼きついたクランク(左側。写真は修正前の様子)を修正して、そのまま再利用。
2,その後、純正新品クランクシャフト(写真右)を表面処理なしで使用。
使用したクランクシャフト以外に違いはない。
ビフォー・アフターのいずれも、ピストンにWPC処理+モリブデンショットのコーティングを施工。
「(クランクの)摩擦の変化だけで、こんなにも音が変わるのか」
という事例でした。
ちなみにこのGSXは、湘南から山梨県まで慣らし走行をしながら、オーナーさんの元へ納車されました。
(まるでレーサーエンジンみたいなレスポンスでした)
前置きが長くなりましたが、表面処理の話に入ります。
表面処理の種類
主にモータースポーツエンジンで用いられる表面処理の一例です。
・ディンプル加工(WPC処理®)
・二硫化モリブデンコーティング(二硫化モリブデンショット/ハイパーモリショット®)
・DLCコーティング
・鏡面加工(3Dラッピング®)
・セラミック(セラコートTM)
・アルマイト(カシマコート®)
・めっき(クロームメッキ、カニボロン® )
上記のうち®マークのあるものは登録商標です。
・セラコート® 鈴木 保利氏(鈴友株式会社 代表取締役社長)
・カシマコート® 株式会社ミヤキ
・カニボロン® 日本カニゼン株式会社
・WPC処理® 株式会社不二機販・株式会社不二製作所・株式会社不二WPC
・ハイパーモリショット®、3Dラッピング® 株式会社不二WPC
なぜ、WPC処理をおこなう会社がたくさんあるのか?
表面加工熱処理法(WPC処理)の特許・商標を取得したのは、愛知県名古屋市にある株式会社不二機販。同社がライセンス許諾した会社が、WPC処理を施工したり、名称を使っています。代理店みたいなイメージですね。
表面処理の活用事例
自動車だと、F-1、軽自動車をふくむファミリーカーやスポーツ車、カーレースに表面処理が採用されています。
バイクはエンジン部品のほか、フロントフォークのインナーチューブにDLCコーティングが使われています。
MotoGPなどレース車両だけではなく、市販車のスポーツモデルにも表面処理が採用されています。
ホンダのメッキシリンダー(NSシリンダー)なども、摩擦損失を減らすための技術、表面処理のひとつですね。
NS(ニッケル/シリコン・カーバイド)メッキによって軽量化と耐焼付性、耐摩耗性において格段の向上をはかりました。
このNSシリンダーはNS500のノウハウをそのまま市販車のNS250F/Rに反映したもので、シリンダーの内壁をニッケル素地にシリコン・カーバイド粒子を分散させた皮膜でコーティング処理しています。これにより、ピストンと同素材のアルミ製一体成型シリンダーを実現。鋳鉄スリーブを持たないので、軽量化はもとより、熱伝導性が良く、放熱効果が向上。さらに、ピストン、シリンダーそれぞれの熱膨張率が同じなので、温度が変化してもピストン、シリンダーのクリアランスが一定に保たれ、安定したパワーが得られます。
https://www.honda.co.jp/factbook/motor/NS250/19840400/003.html
ピストン
いわゆる有名どころのメーカー製ピストンに、表面処理が採用されています。
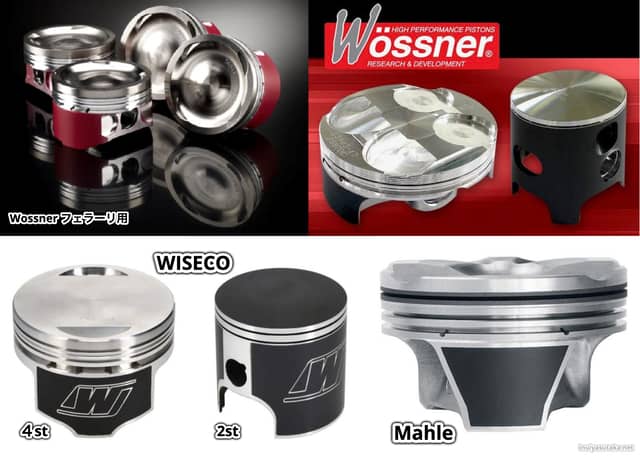
ワイセコ(アメリカ)、ヴォスナー/マーレ(ドイツ)
Ferrari用をのぞいて、どれも黒っぽくて、同じようなコーティングに見えますが、各社、独自の技術を開発しているようです。
ワイセコの2ストピストンはKTM社 現行モデル用です。1970年代〜1990年代の2ストに表面処理をおこなうことは大いに有効かと思われます。
(くわしくは後ほど)
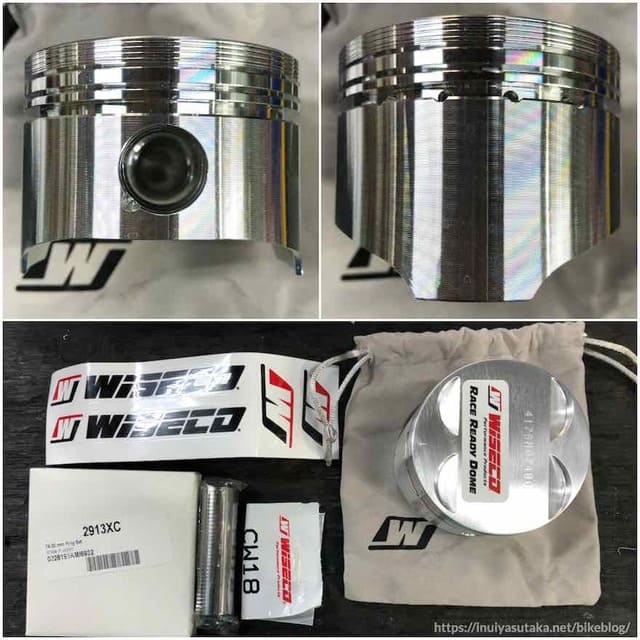
同じワイセコでも、カタナ用(空冷)はピストンスカートに真横の溝が入っています。
前出のピストンと手法は異なりますが、油膜を保持しやすくしているのだと思います。
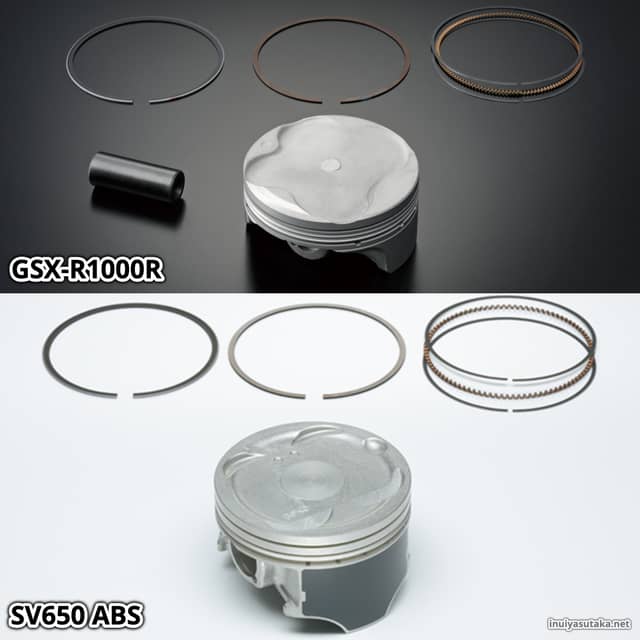
GSX-R1000R(2023年モデル)のピストンピンにはDLCコーティング。SV650ABSのピストンスカートにはレジンコートを施し、ピストンとシリンダーの摩擦を低減しています。
スズキ
ピストンリング
TPR株式会社(旧称 帝国ピストンリング株式会社)がピストンリングや、シリンダーにDLCコーティングを使用しています。
TPRはピストンリング製作の草分け的な会社。1939年1月に日本海軍に対し、ゼロ戦(零式艦上戦闘機)「金星」エンジンの試験用ピストンリングを提出。
2位の米国製品を大きく引き離す試験結果を出したことにより、「田中ピストンリング株式会社」を設立。自動車・バイクのピストンリング、シリンダーライナーなどを製造・販売するようになった。
(現在はどうかわかりませんが)かつて国内バイクメーカーの純正ピストンリングはTPR製か、株式会社リケン製の2社だったと聞いたことがあります。
リケンはリングにクロームメッキを、TPRはDLCコーティングを採用していることが、それぞれ公式サイトで公開されています。
さまざまな研究論文を読んでみましたが、メーカーは私たちが想像もつかないぐらい、あらゆるテストをおこなっていて、きちんとデータ(数値)をとっています。
そのなかで比較的、効果のある箇所・方法で表面処理をおこなっているようです。
フロントフォークや、キャブレターのスロットルバルブなど、エンジン関連パーツ以外にも、表面処理が活用されています。
WPC処理とは?
WPC処理はディンプル(くぼみ)加工の一種。よくゴルフボールの表面に例えられます。
ただ、ゴルフボールとちがい、肉眼では見えないごく小さなディンプルを形成します。
WPC処理®とは、金属製品の表面に微粒子を圧縮性の気体に混合して高速衝突させることで表面が改質する技術です。
株式会社不二WPC
表面が改質すると高硬度化して表面を強化すると同時に、表面形状が微小ディンプルへ変化するので摩擦摩耗特性を向上させます。
たとえるなら、刀鍛冶がハンマーで刀をたたいて鍛えるように、こまかい粒子を高速で吹き付けることによって、焼き入れ効果による高密度化がはかれるそうです。
高密度化とは、フワフワのおにぎり(米と米のあいだにすき間がある)を、ぎゅっと握る(すき間が小さくなる)イメージですね。
エンジンのピストンによく用いられるのがWPC処理で、ディンプルにオイルが入り込むことによって摩擦が減り、耐摩耗性が向上したり、耐焼き付き性が向上するとされています。
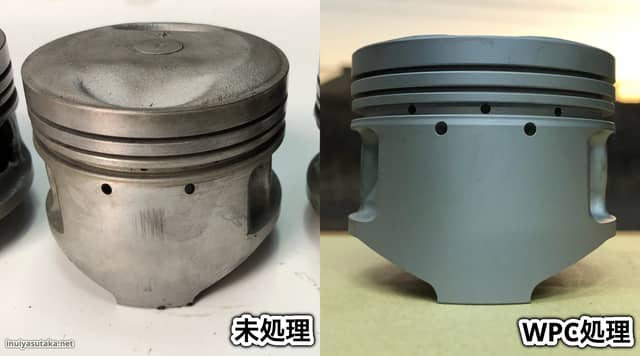
WPC処理したピストン。見た目には「きれいな灰色になった」ぐらいしかわかりませんが・・・
表面の拡大写真(3,000倍)
球状の研磨材にてWPC処理®を行うことにより、円弧状の凹部となり表面張力を助長し、油膜切れを防止します。さらに表面が面圧に耐える強化された組織となり、油膜を保持し、無接触に近くなり摺動部の摩耗を防止します。
株式会社不二WPC
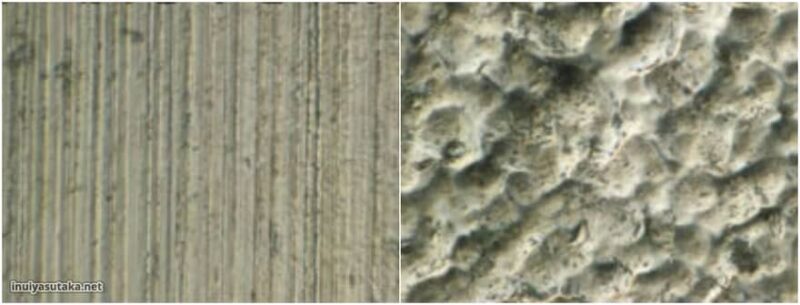
未処理 Rz 0.3 ※肉眼では鏡面/WPC処理®済 Rz 1.6
株式会社不二WPCが公開している資料を見ると、Rz(最大高さ粗さ)という客観的なデータで変化していることがわかります。
WPC処理の効果
実際に目で見て、効果のほどを確かめてください。
WPC処理 驚異のフリクションロス低減
筆者も実際に回して、試しました。
回してみると、おもしろいほど何の抵抗もなく、スルスルッと回転します。
「サビだらけのドライブチェーンを新品に交換して、バイクの後輪がよく回るようになった感じ」
といえば、イメージしやすいでしょうか。
回転しつづける時間が長いことに、気づかれたと思います。逆にフリクションが大きいと、回転しにくく、回転しても回り続ける時間が短くなります。
WPC処理と従来の表面処理のちがい
ピストンの摩擦を減らすコーティング手法の歴史をさかのぼると、二硫化モリブデンなど固体潤滑剤の塗布、すずメッキ、コーティングなどがありました。
ただ、効果が少なかったり、剥がれるなどして効果の持続性に課題がありました。
それで考案されたのがWPC処理。
ピストンに上塗りするのではなく、ピストン表面を改質して、オイル保持できるようにしたのです。
ちなみに、先ほどお伝えしたとおり「WPC処理」という名称は登録商標です。なので、他社が無断で同じ名称を使って、同様のサービスを提供することはできません。(製法特許も取得されています)
ただ、ショットピーニングの原理を用いた表面処理加工は、各社が独自の名称を使っておこなっています。
WPC処理はショットピーニングの発展系とされています。
WPC処理の使用例
さかのぼって発見できたもので一番、古いのは1997年。
7月に発売されたホンダのモトクロッサー「CR 250R/125R」のトランスミッションに、WPC処理が施されている旨が記載されています。
●ミッション3速ギアの歯元にショットピーニング処理追加(WPC処理)
https://www.honda.co.jp/factbook/motor/CR/199907/CR_008.html
またホンダ初のハイブリッドカー「インサイト」(1999年発売)にショットピーニングの技術を採用した旨が記録されています。
(本田技研R&D「表面改質によるエンジンのしゅう動抵抗低減技術」)
WPC処理は自動車・バイクのピストンにも採用されていますが、具体的な車種名や、箇所はあまり公開されていないようです。
ただ、4ストロークの旧車はもちろん、2ストロークにも愛好家の間でWPC処理がよく使用されています。
筆者の中ではエンジンに用いられる表面処理の中で、WPC処理がもっともメジャーな気がします。
WPC処理したトランスミッション
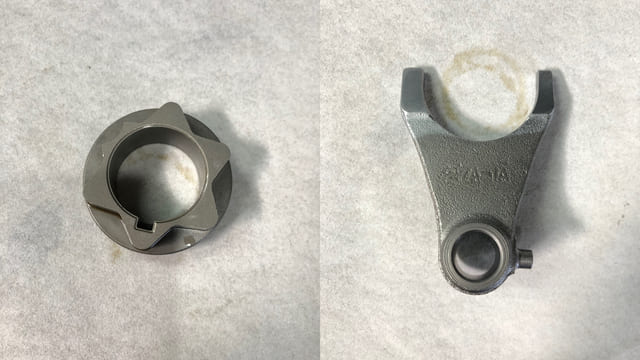
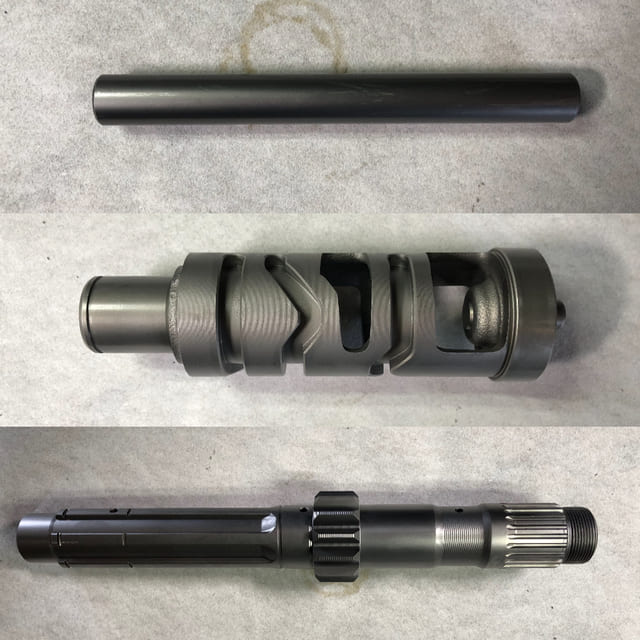
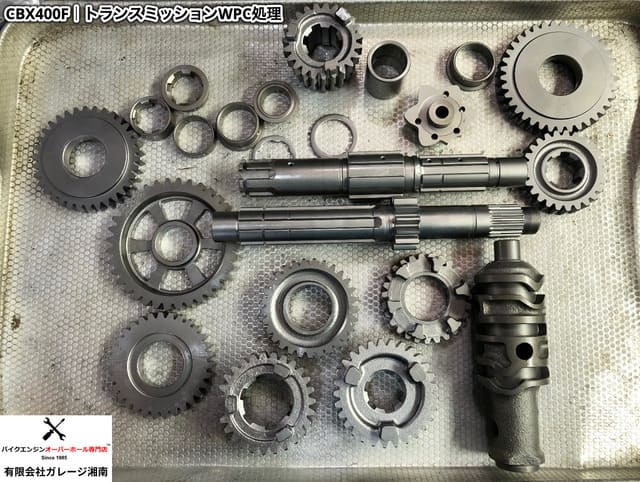
WPC処理したクランクシャフト
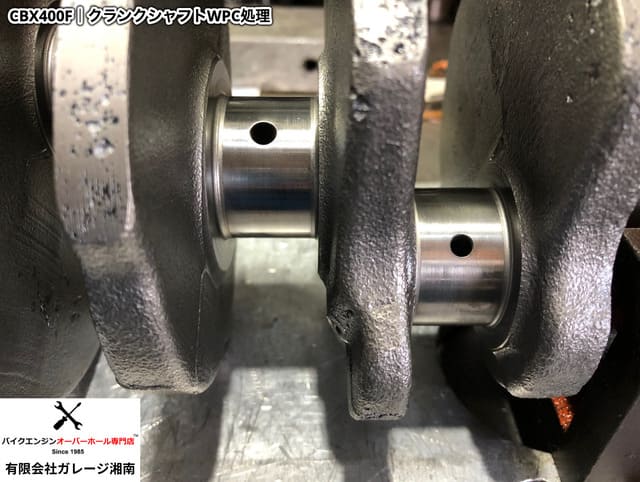
※いずれも筆者撮影
キャブレターのスロットルバルブ
湿度が高くなると、スロットルバルブが張りつきやすくなります。
症状としては、エンジンが完全に暖まっていない状態で、スロットをある程度、開けると、スロットルを戻しても開けた状態のままになる、というものがあります。
つまり、加速して、スロットルを戻してもエンジンの回転が下がらず、加速したままの状態。
筆者は2ストロークで何度も経験していますが、けっこう危険です。
こうしたスロットルバルブの張りつきや、摩耗を抑制できるのであれば試してみたいものです。
WPC処理の向き・不向き
WPC処理は、清掃する(言い換えると裸にする)という意味があります。
WPC(Wide Peening and Cleaning=清掃するの意)
つまり処理をおこなうと、油分がキレイさっぱり剥がれ落ちます。だから加工後すぐに、防錆の油を付着させる必要があるそうです。
実際、筆者がWPC処理を依頼して納品された部品にも油が付いてました。
(錆びてしまうので注意するよう説明書きがありました)
処理をおこなった部分が外に露出して、油分が無くなってしまうような部品は、材質や状態によっては錆びてしまうため、WPC処理が不向きなケースもあるようです。
逆にエンジンやミッション、グリスなど油分がついたままの状態を維持できる部品は、錆による心配はなさそうです。
WPC処理の耐久性は?
耐久性については性質上、高熱が加わる部分や、当たりがきつい箇所は、だんだんと効果が落ちてくるそうです。
たとえばエンジンパーツですね。
ただ、具体的に「何キロまで持つ」とまではハッキリわからないそうです。まぁ、当然ですね。
「エンジンって何㎞で壊れますか? どのくらいまで持ちますか?」
という質問をするのと同じで、ケース・バイ・ケースだからです。
同じバイクで、同じ地域を走っても、ライダーによって扱い方・乗り方が違うため、まったく同じ状態にならないのが通常です。
たとえばシリンダーのクロスハッチ。
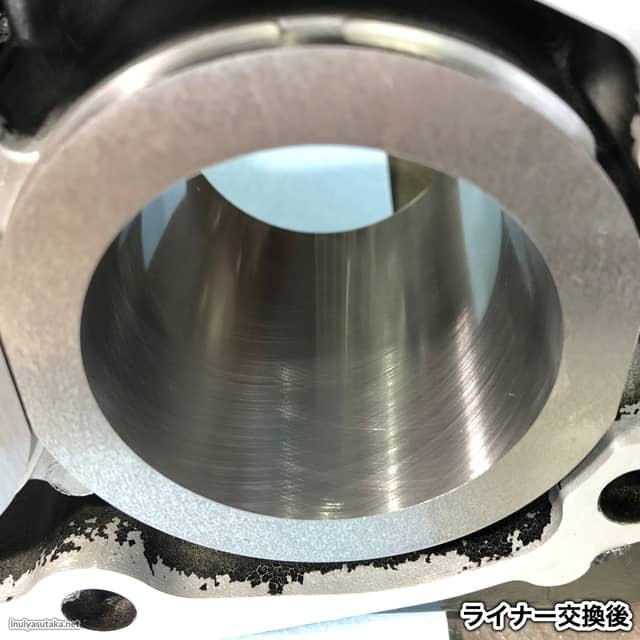
クロスハッチは何のためにある?
高温で摩擦するシリンダーでは、潤滑不良による焼き付きが起きやすくなります。
潤滑不良を防ぐために、シリンダー壁にエンジンオイルがくっついた状態になっていることが望ましいです。一見、こまかい傷のように見えるのが、クロスハッチと呼ばれるオイル溜まりです。
クロス(X)状にすることで、シリンダー壁にオイルが留まりやすくなるわけです。
走行距離を重ねるごとに、クロスハッチは少しずつ摩耗していきます。
ですが「何キロ持つの?」と言われると、ケース・バイ・ケースとしか答えようがないです。
実際には走行距離のわりにピストンや、シリンダーの傷や摩耗が多かったり、その逆もあります。いちがいに走行距離だけで判断できない部分があります。
WPC処理も、諸条件によって効果の持続性に差があると思われます。
ヨーロッパ車などは、ユーザーが「慣らし運転」をおこなわないため、慣らし運転に相当する距離だけ表面処理の効果が持てばいい、という考え方もあるようです。
WPC処理の注意点
WPC処理にかぎらず、表面処理には部品の寸法が変わるものがあります。
WPC処理:1ミクロン(1/1,000mm)のマイナス公差
表面処理によっては、もっとプラスになるものもあります。ですのでエンジン部品に表面処理をおこなった場合、条件次第でクリアランスがおおきく変わることがあります。
つまり、きちんとクリアランスを管理してエンジンを組まないと最悪の場合、焼き付きます。
「表面処理をしたから、クリアランスなんて気にせず組んでも大丈夫」
ではありませんよ、という話。過信は禁物です。
ちなみにWPC処理や、DLCコーティングなど表面処理は、レースをやっていたり、エンジンのオーバーホールを専門にやっているショップ以外、くわしく知らないと思います。
お店の方に「バイク屋なのに何で知らないの?」とか言わないように笑
高熱になる箇所には?
ハイパーモリショットが適しているようです。
ハイパーモリショットとは、「二硫化モリブデンショットにナノ粒子を添加したもの」。長時間、高回転・高温で使用する部品に適しているとされています。
鈴鹿8耐などレースで使われている技術みたいですね。WPC処理もそうですが、ミッションがスムーズに入るようになるそうです。
旧車にお勧め 二硫化モリブデンショット
旧車・絶版車のエンジンオーバーホール現場では
「やむなく部品を再使用する」
「中古部品を探すしかない」
という場面が日常的にあります。というのは、1970年〜1980年代のバイクはもちろん、1990年代から2010年ぐらいのバイクは純正部品が廃番になりつつあるからです。
(運良く部品が見つかっても、部品代が異様に高騰していたり、数ヶ月待ち・納期不明だったりします)
中古部品については、まともに使えそうな部品が少ないです。
そこで純正部品や、社外部品が出ない旧車の場合、表面処理を用いてピストン、カムシャフト、クランクシャフト、コンロッド、メタルなどを再生し、再利用しています。
それが二硫化モリブデンショットです。
二硫化モリブデンショットの効果
ピストンなどに使用される一般的な二硫化モリブデンコーティングは、バインダー(接着剤などの結合剤)を使用するため耐久性(効果の持続性)が課題とされてきました。
不二WPC社によれば、WPC処理後に、バインダーを使わない二硫化モリブデンショットを使用することで長期間、低摩擦効果が持続するといわれています。
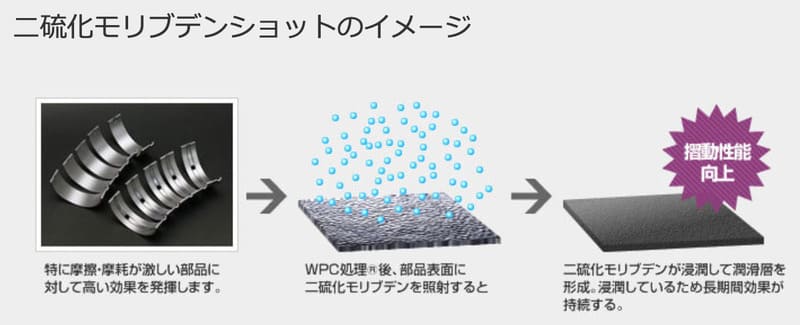
以下、ホンダの実験による結果です。
ピストン単体でフリクション50%低減!
自動車メーカーの実験で、ピストンスカートに各種の表面処理を施し、エンジン単体をモーターリングしてフリクションを比較しました(1L・3 気筒エンジン、部分負荷)。二硫化モリブデンコーティングは、フリクション低下率が1.4%であるのに対して、マイクロディンプル処理で2%、二硫化モリブデンショットは5%の低下率を示す結果が得られました。
株式会社不二WPC
高い摺動抵抗低減効果が認められ、市販車で採用!
自動車メーカーの量産車のエンジンでは、1999年からピストンリングのトップリングとピストンのスカート部にマイクロディンプル処理が行われ、2001年からは、二硫化モリブデンショットが量産採用、ピストンスカートに11µm 径の高純度二硫化モリブデンが打ち込まれました。この二硫化モリブデンは表面から少し深い層(4µm)まで入り込み、100 時間耐久試験後の摩耗状態でも二硫化モリブデンが残るとともに、摩耗後も二硫化モリブデンが残存し、フリクション低減効果が維持されていることが確認されました。
株式会社不二WPC
これにより、ピストン単体でのフリクション効果は50%に達し、自動車の低燃費化に大きく貢献、高い評価を得ました。
二硫化モリブデンショットの使用例
二硫化モリブデンショットは、部品の厚みを増すことができます。つまりある程度、クリアランスを調整することができるわけです。
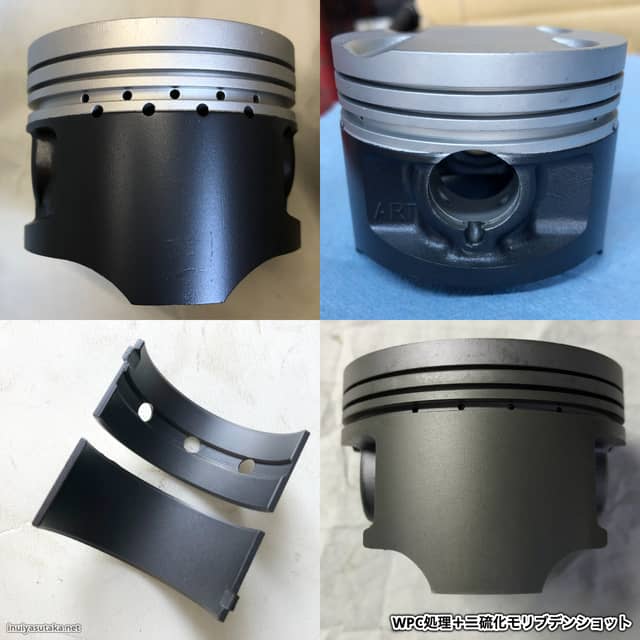
純正部品が廃番、社外品もないため、使用済みピストンにWPC処理+二硫化モリブデンショットを施した例。クランクメタルにも同処理をおこなっています。
WPC処理だけをおこなう場合より若干、コストはかかりますが、部品を入手できない場合や、より耐久性を持たせたい場合は十分、検討の余地はあると思います。
以下のショップで検証済みです。
二硫化モリブデンショットの耐久性
効果の持続性については、WPC処理と同様、諸条件によって変わると思います。
WPC処理+二硫化モリブデンショットをほどこして組んだエンジンを走行後に分解して検証したところ、当たりの強い部分はコーティングが減っていました。
(完全に剥がれているわけではない)
つまりコーティングが緩衝材になっているわけです。
WPC処理と二硫化モリブデンショットの使い分け
いろいろな考え方があると思いますが、中古パーツに処理する場合、摩耗が進んでいる部品には二硫化モリブデンショット。
それほど摩耗していない部品は、WPC処理のみにすることがあります。
新品部品や、比較的、予算が許す場合はDLCコーティングを使うのもありだと思います。
CBR1000RR-Rの表面処理
CBR1000RR-Rの純正ピストン(高強度アルミ鍛造)のスカート部分には
オーベルコート®
というコーティングが施されています。テフロンとモリブデンがベースの特殊コーティングのようです。
ピストンスカート部にオーベルコートのコーティング、ピストンピンのクリップ溝にニッケル-リンめっきを施すことで高回転に対応した耐摩耗性を確保し、高回転化の実現に寄与している。
https://www.honda.co.jp/CBR1000RRR/powerunit/
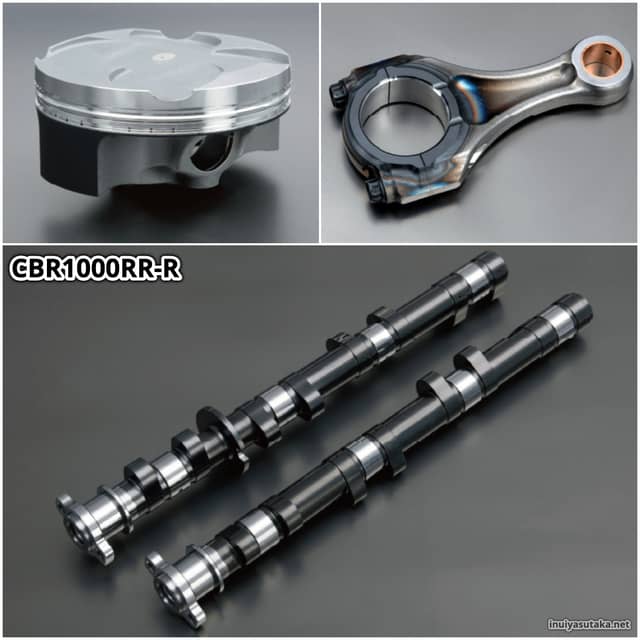
DLCコーティングされたCBR1000RR-Rのカムシャフト。黒い部分が処理されている箇所です。
市販車のカムシャフトにDLCコーティングが採用されるのは世界初だとか。
バルブ駆動ロスを低減させる
DLCコーティングを施したカムシャフト。https://www.honda.co.jp/CBR1000RRR/powerunit/
RC213V-Sと同様にDLCコーティングを施したカムシャフト。フィンガーフォロワー式のロッカーアームの採用とあわせ、DLC未処理の物と比べバルブ駆動ロスを約35%削減している。
チタン製コンロッドの大端部にも、DLCコーティングがほどこされています。
DLCコーティングとは
DLCコーティングは表面処理の中で比較的、あたらしい技術です。
ダイヤモンドと、グラファイト(黒鉛)の特性の中間的な材料とされています。
ダイヤモンド:高硬度、摩擦係数が低い
グラファイト:えんぴつの芯に使われているように潤滑性能に優れる(ただし脆く壊れやすい)
DLCは耐摩耗性、摺動性(低摩擦で滑りやすい)、耐食性に優れている、摩擦時の攻撃性が低い、化学反応が起きにくいなどの特徴があります。
DLC (Diamond-Like Carbon)コーティングとは、主に炭素と水素で構成される、ナノレベルの薄膜を金属表面にコーティングする技術です。このコーティング層は、非常に薄いにも係わらず硬質な性質を持つため、従来にない低摩耗・高潤滑性をもたらします。
不二WPCでは、DLCコーティングにWPC処理®を組み合わせる技術開発に成功。DLCコーティングとWPC処理®を組み合わせることで密着性を高め、さらにその効果を長期間持続させることができます。株式会社不二WPC
高等研究機関でその優れた性質が証明されている現在、数多く存在する表面処理加工において、最高の技術として認知されつつあります。
不二WPCが開発・特許を取得したこの技術は、低摩擦性・高耐久性・高硬度性・耐腐食性などにおいて、最も高い効果を得ることができる、最新の表面処理技術です。
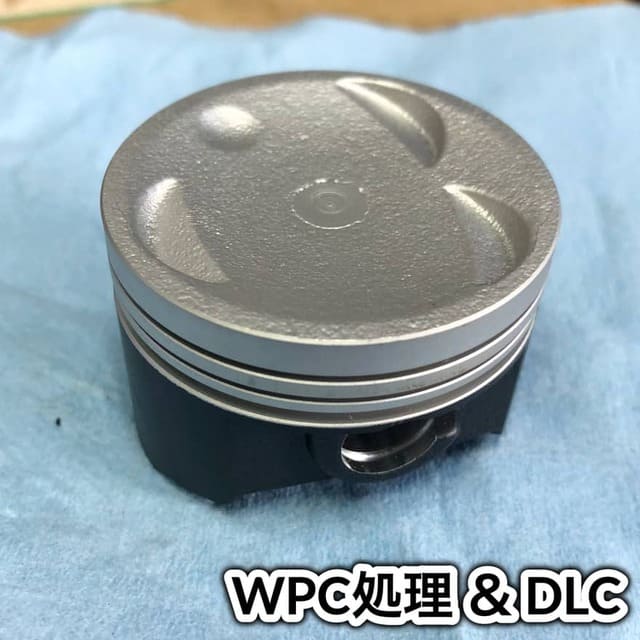
不二WPC社でWPC処理後、DLCコーティング(黒い部分)したピストン。
DLCコーティングでおさえるべきポイントは、「DLCにもいろいろな種類がある」ということです。
たとえば住宅の場合、大きく分けると「木造」と「鉄筋」があります。さらに木造住宅にも「在来工法」や「ツーバイフォー」など、種類があります。
また同じ「在来工法」の家でも、設計会社によって特色があります。
DLCコーティングも施工する会社(工場)によって特色があり、仕上がりが変わってきます。「どこへ頼んでも同じ」ではないんですね。
プラス、処理をおこなう部材の状態によって仕上がりが異なるようです。
わかりやすくいうと、新品のカムシャフトと、それなりに使い込まれたカムシャフトでは、もともとの状態がちがうため、仕上がりも変わるということです。
ちなみに、これまでに紹介したほかの表面処理と比較して、DLCコーティングは費用が高めです。
DLCコーティングの使用例
さきほどのCBR1000RR-Rのカムシャフトや、チタン製コンロッド大端部にはDLCコーティングが採用されています。
ホンダ公式サイトにあるとおり、市販車にDLCコーティングを採用したのはMotoGPからのフィードバックでしょう。
本田技研の文献によると、F−1エンジンのロッカーアーム、カムシャフト、トランスミッションなどに自社で独自開発したDLCが採用されているようです。
そのほか日産マーチ、全日本選手権ロードレースJ-GP3で使用されるマシンのエンジンにも、DLCコーティングが用いられています。
さきほどお伝えしたように、DLCコーティングもさまざまな種類があり、まだまだ科学的に未知な部分も多く、素材や箇所、用途などによって、向き不向きがあるようです。
こうした不確定な要素があるものの、比較的、効果の大きい箇所や用途、処理方法などが検証により、解明されつつあるのでホンダのみならず、スズキやドゥカティなど、各社がDLCコーティングを採用しているのだと思います。
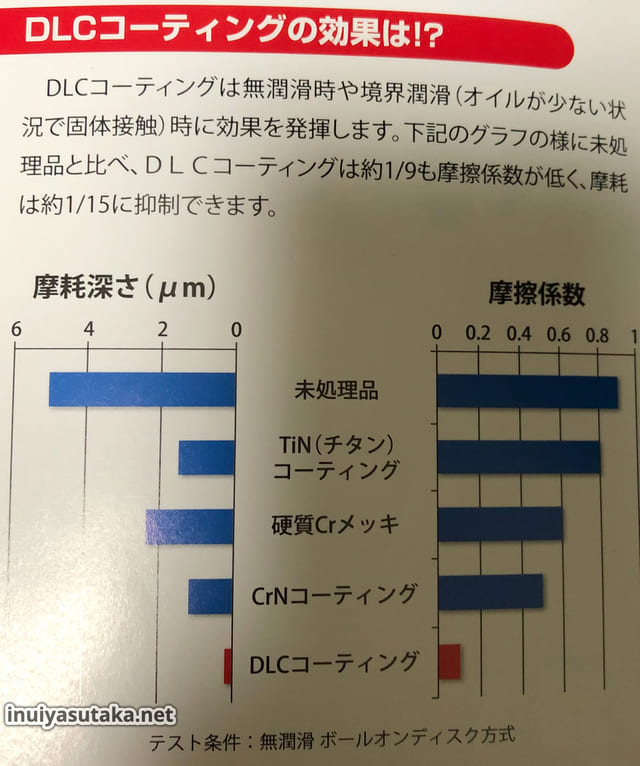
DLCコーティングに不向きなもの
当然ながら、デメリットもあります。
導電性のない材質や、カーボン(炭素)と反応しない材質はコーティングできません。
導電性(どうでんせい)とは?
https://www.weblio.jp/
電流が流れやすい性質。物質などで、電気伝導を生じやすい性質を指す。
DLCコーティングに適さないもの例
アルミ(レース車両以外のピストン、メタル等)、鋳鉄部品(シリンダー、カム、ピストンリング(2ストや4ストのセカンドリング等)、銅(ブッシュ)、焼結部品(オイルポンプ)
※メッキの場合、コーティングできますが、剥がれる場合があります。
2ストロークの場合、ピストンにDLCコーティングすると剥がれ落ちることがあるため、不向きなようです。
2ストエンジンのピストンピンへのDLCについて
https://www.ne-jp.com/wpc/page/3pricelist/index.html
DLCは非常に硬い膜ですが、1箇所に集中して力がかかる環境に弱い傾向があります。2ストはコンロッド小端にローラーベアリングを使っており、このローラーが強い力でピストンピンにかかるので剥離の可能性がございます。 その為2ストはWPC+ハイパーモリショットをおすすめしています。
本田技研の文献にも、「従来のDLCでは高圧で1箇所に力が加わると同じ現象が課題」とされていました。
そこで改良を加えたDLCを開発し、トランスミッションなどに採用したそうです。
(本田技研「カムシャフト,ロッカアーム DLC コーティングの開発」)
DLCコーティングの注意点
メリットの裏返しで、化学反応しにくいためオイル添加剤(とくにモリブデン系)の使用は控えた方がよさそうです。
(くわしく知りたい方は、DLCの種類を調べると根拠が見つかると思います。複雑な話になるのでここでは省略)
もう一つ、DLCコーティングされた箇所はオイルが食いつきにくいので、エステル系エンジンオイルの使用が推奨のようです。
逆にいうと、オイル添加剤を使わないようにして、エステル系エンジンオイルを使用すれば問題ないでしょう。
ダイクロン コーティング
千代田第一工業株式会社が開発した、世界初の硬質炭化クロムめっきの表面処理技術。
JIS規格の硬質クロムめっきと比較して、ダイクロンは優れた耐摩耗性・耐焼き付き性・低摩擦係数を持つといわれています。
ダイクロン主な特徴
1,耐摩耗性に優れる
2,耐焼き付き性に優れる
3,母材との密着性に優れ、亀裂や剥離がしにくい
4,クラックが微少なため、耐浸食性に優れる
5,ミクロン単位の厚さ調整が可能にする肉盛加工
6,ダイクロンは、幅広い材料にコーティングが可能
7,一般砥石での容易な研磨・研削加工が可能
くわしくは公式サイトで確認していただくとして、ピストンなど、エンジンパーツへの使用した場合のメリットを挙げてみます。
摩擦面の摩擦係数を減らす
凝着や焼付きは、摩擦によって生じる摩擦熱によって発生します。ダイクロンは摩擦係数μ=0.1~0.5を示し、他の硬質クロムめっきや窒化処理と比べて、低い摩擦係数を示すことがわかっています。 また、ダイクロンは熱に対しても非常に強い特性をもっており、ダイクロンの表面に生成した皮膜(Cr+Cr23C6)が摩擦熱によって(Cr2O3)に変態し、非常に強い不動態皮膜を形成したことにより、金属間融合を防いだものと考えられます。
https://daikuron.com/seizeresistance/
単純比較はできないと思いますが、前出のDLCコーティングと同等の低い摩擦係数です。
ダイクロンの密着性
ダイクロンめっきの最大の武器といっても過言ではない「密着性」の高さ。この密着性の高さをご評価いただき、製缶メーカー様・飲料メーカー様・製薬メーカー様等の製造ラインにおいて、ダイクロンめっきを施した部品が導入されています。
ダイクロンはめっき層と母材金属との密着力を強化するために、独自開発の混合触媒を用いることで、分子間結合力の高い炭化クロム複合金(Cr+Cr23C6)によって強力に密着されています。
従来の硬質クロムめっきとダイクロンを折曲げ試験によって確認してみると、両者とも折り曲げ角度90℃でクラックが生じ、硬質クロムメッキは母材までクラックが生じます。 一方ダイクロンは数度折り曲げを繰り返しても、クラックの成長が認められるものの、剥離はおこしません。
残念ながらめっきの密着性を評価する試験法が確立されていないため、具体的な数値で密着性の高さをお示しすることができません。しかし、ご利用いただければハッキリとその差を実感できるものと自負しております。
https://daikuron.com/adhesion/
どんなに優れたコーティングも、すぐ剥がれてしまっては意味がありません。
ダイクロンの密着性の高さはDLCコーティング以上とされています。
ミクロン単位の厚さ調整が可能にする肉盛加工
ダイクロンは1~200μの間で厚さを処理可能です。 機器のわずかな寸法不足、冶工具の摩耗部分の肉盛り加工などにご好評頂いております。 図7は、標準的なダイクロン処理のコーティング厚になります。
https://daikuron.com/daikuron/
エンジンで重要なクリアランス。
ミクロン単位でコーティング層の厚さを調整できる、という事は大きなメリットです。
旧車の場合、社外ピストンがあればまだいいほうで、部品が手に入らない事がよくあります。鋳造ピストンで、部品を再利用せざるを得ない場合、ダイクロンを検討するのもいいかと思います。
(ダイクロン処理後、8万km走行したピストンを観た上での意見です)
「二硫化モリブデンショット」とどちらが適しているか、興味深いところです。
ピストンヘッドへのコーティングと効果
主に自動車エンジンのピストンクラウンに、セラミックや、アルマイトをコーティングしているのをよく見かけます。
(英語圏では「ピストンクラウン」といいます)
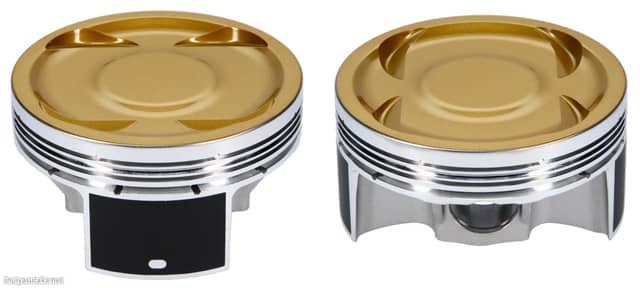
ドラッグレースなど、高馬力エンジンのカーレースで、混合気(ガソリンと空気)が薄いことによりピストンクラウンが軟化。
ピストン破損を防ぐ熱対策として、セラミック クラウンコーティングが用いられるようになったようです。
熱の移動には、対流、伝導、放射の3つの方法があります。対流は、空気、水、その他の中間的な液体や気体が、熱源からより低温の場所に熱を運ぶときに起こります。伝導は、熱が固体の中を直接移動することです。そして輻射は、太陽が照りつけるように、赤外線によって物体を加熱することです。
燃焼室では高温のガスが渦を巻き、放射された熱はピストン・クラウンに吸収され、伝導によって外部に移動し、最終的にはリング、オイル、シリンダー壁へと伝わります。
筆者訳
https://www.enginebuildermag.com
日本でもバイクのピストンクラウンに、セラミックコーティングを採用しているケースが見受けられます。
比較的、日本でよく知られるセラミックコーティングが、セラコート。
アメリカのNIC社が開発したセラミックを主成分とするコーティングです。
ピストンクラウンに施工するピストンコート、スカート部分に施行するマイクロスリックなど、用途に応じて種類があるようです。
セラコートの例
有効性について、研究論文には以下のようにあります。
(あくまで概要のまとめなので、学生さんや、研究者の方は元の論文を参考にしてください)
・燃焼室のセラミックコーティングによって、熱損失が16.2%削減されました。
・排気バルブのセラミックコーティングによって、熱損失が18.7%削減されました。
・セラミックコーティングによって、燃焼室内の平均温度が約25℃低下しました。
・セラミックコーティングを施した場合、NOx排出量が10〜12%、CO排出量が約20%削減されました。
燃焼室と排気バルブにセラミックコーティングを施した実験では、コーティングが施されていない場合に比べて、燃焼効率が向上し、NOxやCOの排出量が減少することが示されています。
また、セラミックコーティングによって燃焼室温度が下がることが観測され、高温時に生じるデトネーション(異常燃焼)の抑制にも効果があることが示唆されています。
さらに、セラミックコーティングが耐久性にも優れているため、エンジン部品の寿命を延ばすことができる可能性があります。
出典:The Effect of Ceramic Coating on the Performance and Emissions of a Spark-Ignition Engine” (J. K. Kim, K. H. Kim, and S. H. Park, SAE Technical Paper 2005-01-1499
実験では、セラミックコーティングを施したピストンクラウンを用いたエンジンと、コーティングを施さなかったピストンクラウンを用いたエンジンを比較しました。
実験結果から以下のような知見が得られました。
・セラミックコーティングを施したピストンクラウンを使用したエンジンでは、トルクが最大で5.1%向上し、最大出力が4.8%向上しました。
・セラミックコーティングを施したピストンクラウンを使用したエンジンでは、平均的な燃焼圧力が増加し、燃焼効率が向上しました。
・セラミックコーティングを施したピストンクラウンを使用したエンジンでは、NOxおよびCOの排出量が減少しました。
・セラミックコーティングを施したピストンクラウンは、高温に耐えられるため、エンジン寿命を延ばすことができる可能性があります。
出典:”Effect of Ceramic Coating on Piston Crown on the Performance of SI Engine” (A. K. Sharma, S. S. Thipse, and S. R. Gupta, International Journal of Engineering Research and Applications, Vol. 4, No. 6, June 2014)
SNSでフォローしていることもあり、筆者はBpナカヤマ さんの施工事例をよく見ています。
ピストンヘッド部にセラコート(ピストンコート)。 スカート部にもセラコート(マイクロスリック)施工!
cerakoteピストンコートは断熱効果が高く、燃焼室内でヒートバリアを形成します。燃焼室の熱を外に出さない、外からの熱も燃焼室に入れないという考え方です。「燃焼室内の温度を安定させるさせる」というのが理念かと考えます!
「マイクロスリック」はスカート部に施工し、オイルとの馴染みが良く、摺動抵抗や摩擦抵抗の軽減に特化します!
実際に弊社で施工したピストンでも、デトネーションを起こした燃焼室でピストンは助かっていた事は多々あります!
レースで、6年酷使したピストンでも剥がれてはおりません!
良い事ばかり書くと胡散臭くなりますが、「オカルトやオマジナイ」では無いのです。世の中にはこういう施工もあるという事を知っていただけば幸いです…
Bpナカヤマ さんFacebookより引用
WPCも、二硫化モリブデンショットも、やがてコーティングが剥がれますから、記事どおりならかなり耐久性が高いと思われます。
今のところ、セラコートがWPC処理や、DLCコーティングほど市販車で広く普及していない理由として、
・塗装のため、塗膜の厚みをコントロールしたり、均一化するのが困難(エンジンクリアランスが管理しにくい)
・適切な施工をするために専門的な技術が必要(施工者によって品質に差が出やすい)
・完成までに時間がかかる
などが考えられます。
余談ですが、セラコートはエンジン表面や、フレーム、スイングアーム、キャブレター、フロントフォークアウターチューブなどにも、よく使われています。
まとめ:失敗しない表面処理の活用法
エンジンにおける表面処理の目的
1,表面を硬くする
2,金属同士の焼きつき防止
3,摩擦係数を下げる
部品の生産過程でおこなわれる処理のほか、今回取り上げた表面処理や、エンジンオイル添加剤も、広い意味では表面処理といえるのかもしれません。
(オイル添加剤には1の効果はないと思いますが)
表面処理の効果や持続性は、そもそもの部品の加工精度や状態、エンジンの組み立て方、使用するエンジンオイル、メンテナンスサイクル、ライダーのエンジンの扱い方、走行環境によって変わってきます。
あとは対費用効果をどう考えるかによっても、表面処理に対するとらえ方が変わってくると思います。
いずれにしても、「表面処理したからエンジンは壊れない」「メンテナンスしなくていい」という魔法の杖ではありません。
あくまで適切なクリアランスでエンジンを組み、きちんとメンテナンスをしたり、適切な扱い方をした上で、よりバイクを長持ちさせるためのもの、だと考えておいた方がいいと思います。
本質から離れないことが大事です。
表面処理技術の可能性
新品部品でも、とくに設計が古いものであれば表面処理する恩恵は大きいと思います。
コーティングは万能ではないため、部品の状態によって施工の可否があります。しかし、溶射技術などと合わせて活用することで旧車修理や、部品を再利用できる可能性が広がったと言えるのではないでしょうか。
表面処理のえらびかた
餅は餅屋。素直に問い合わせるのが確実だと思います。
どの表面処理が適切か、向き・不向きを、すべて私たち一般人が判断するのは不可能だからです。
材質や目的、箇所によって向き不向きがあったり、効果の持続性が異なったり、加工する母材の下地処理によって仕上がりが変わってきます。
エンジンパーツのすべてをコーティングするのは莫大な費用がかかってしまうので、パーツの状態や優先順位、目的を決めた上で、必要な箇所にコーティングするのが現実的だと思います。
この手の情報はググっても、AIに聞いても答えは見つからないと思うので、その道のプロに聞くのが早いです。
関連する研究論文・資料
・超短パルスレーザーによるピストンリングの テクスチャリング加工が摩擦力に及ぼす影響
・自動車用シリンダボアのディンプル状マイクロテクスチャによるピストンリングの摩擦低減
・内燃機関用ピストンスカート部への固体潤滑剤付与技術とその効果
・本田技研工業 内燃機関用ピストンに関わるトライボロジー技術の最近の話題
・内燃機関用ピストン表面処理技術の開発
・4サイクルガソリンエンジンのコンロッド軸受焼き付きに関する潤滑性の考察